Product Category
RELIANTT Machinery
COMPANY
Reliantt company is the leader of China metallurgical machinery field. Relying on “constant innovation, high quality, superior service” philosophy, we have developed rapidly in the past few years. With numbers of experienced technicians, advanced technology and processing equipment, our products are with professional design, advanced technology and reliable quality, and exported to more than 100 countries.
Manufacture & Export Experience
Production Personnel
Service countries and regions
RELIANTT Machinery
NANTONG RELIANTT Machinery Co., Ltd., engaged in manufacturing and exporting roll forming machine, tube mills, cut to length line, slitting line etc for more than 30 years.
With more than 180,000 square meters and 800 workers for the plants, we are able to provide powerful guarantee for product quality and date of delivery. At the mean time, we have professional research and development center as well as more than 250 sets large and medium-sizes processing equipment... ...
RELIANTT Machinery
Our supplied machines are mostly used in the steel structure construction field (such as stadium, convention and exhibition center, residence ) , as well as auto product and energy field etc.

Project

Project

Project

Project
RELIANTT Machinery
Exhibition & Information
RELIANTT Machinery
With more than 30 years experience, our produces have been exported to more than 100 countries and regions: America, Eastern & Central Europe, Middle East, Africa, Southeast Asia etc. We are prestigious for our competitive price & quality products.
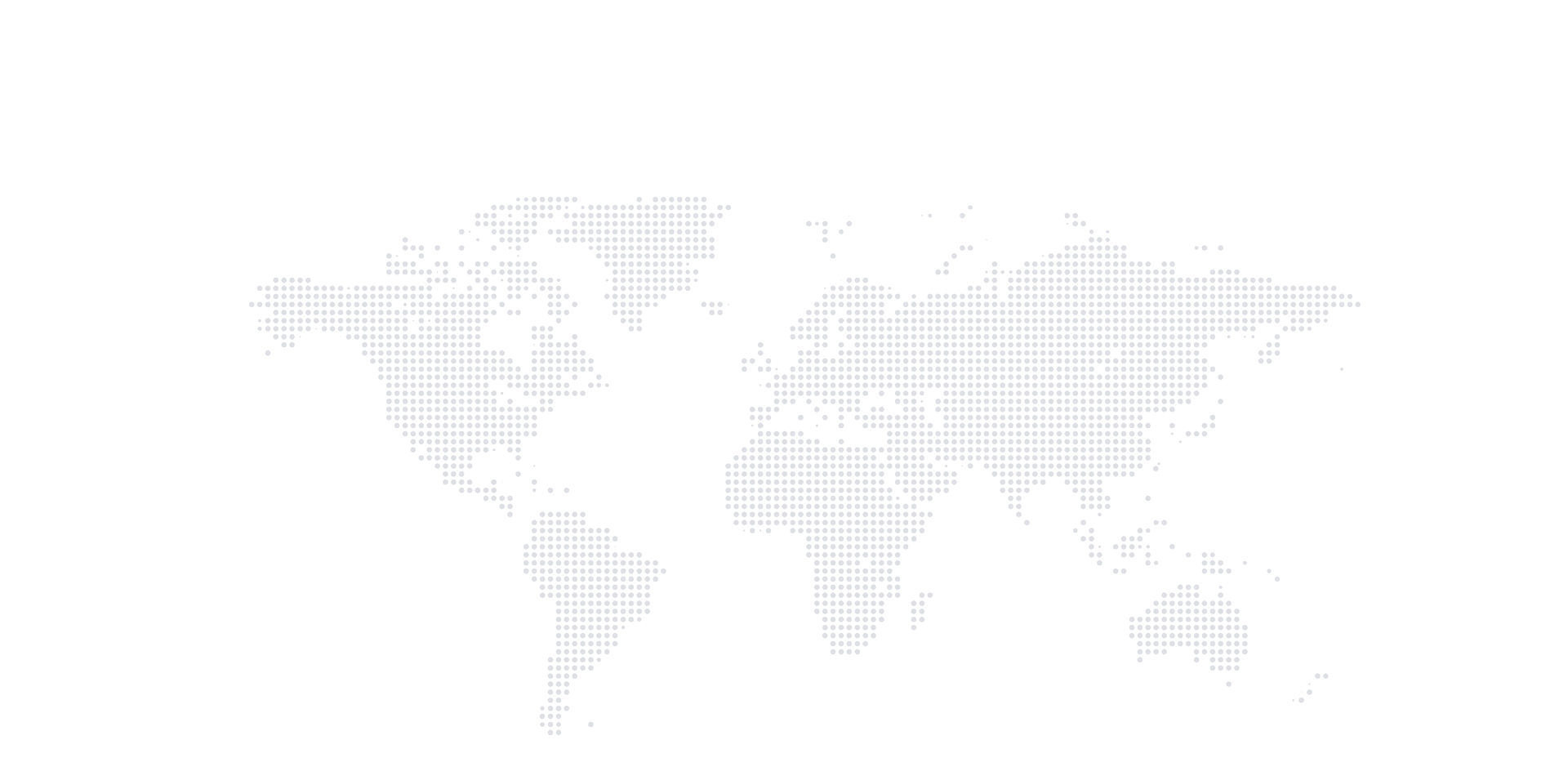